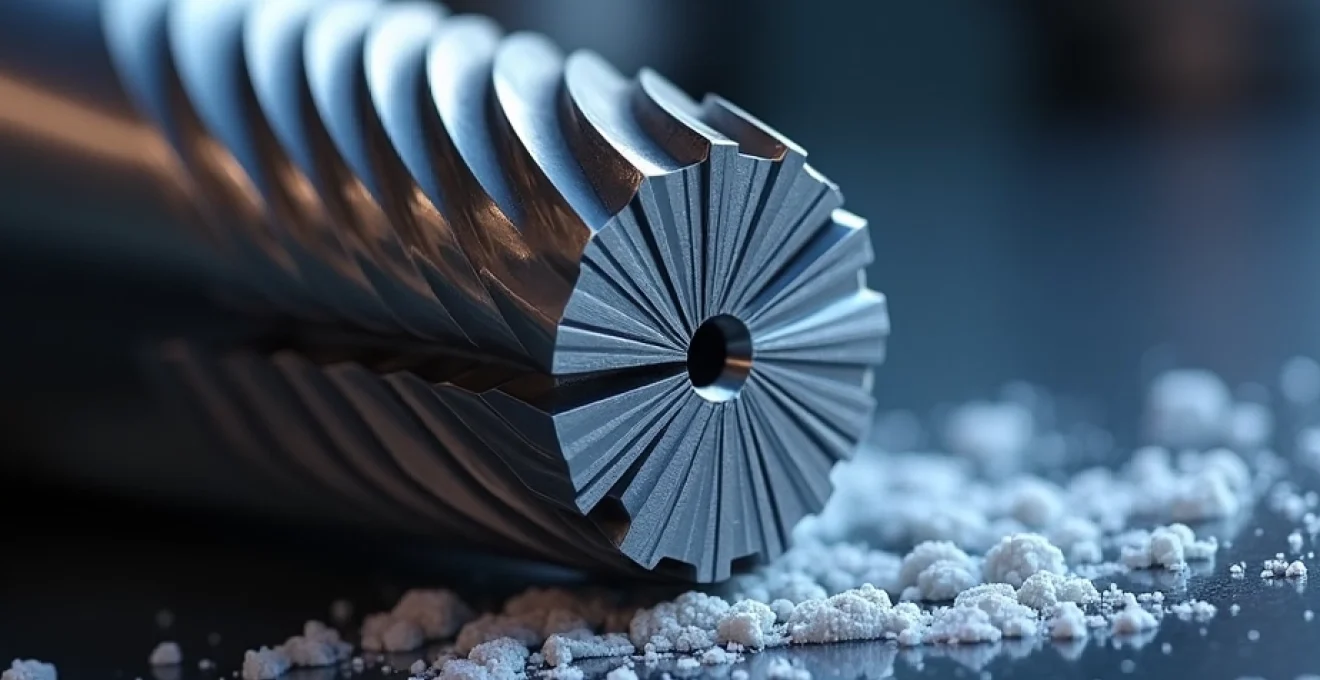
L'usinage de pièces mécaniques complexes requiert une précision sans faille pour garantir des performances optimales dans les industries de pointe. Que ce soit pour l'aérospatiale, l'automobile ou le médical, la maîtrise des techniques d'usinage de haute précision est devenue un enjeu stratégique. Les avancées technologiques en matière de machines-outils à commande numérique, d'outils de coupe et de logiciels de conception ont ouvert de nouvelles possibilités pour repousser les limites de la précision. Cependant, optimiser cette précision reste un défi qui nécessite une approche globale et une expertise pointue. Explorez les méthodes et technologies de pointe qui permettent d'atteindre des tolérances toujours plus serrées dans l'usinage de pièces mécaniques complexes.
Principes fondamentaux de la précision dans l'usinage CNC
L'usinage CNC (Commande Numérique par Ordinateur) repose sur des principes fondamentaux qui conditionnent la précision finale des pièces. Au cœur de ces principes se trouve la stabilité de la machine-outil. Une structure rigide et des guidages de haute qualité sont essentiels pour minimiser les vibrations et déformations pendant l'usinage. La précision du positionnement des axes est également cruciale, avec des systèmes de mesure au micron près.
Un autre aspect fondamental est la maîtrise des conditions de coupe. La vitesse de rotation de la broche, l'avance de l'outil et la profondeur de passe doivent être optimisées en fonction du matériau usiné et de la géométrie de la pièce. Une gestion fine de ces paramètres permet de réduire les efforts de coupe et d'améliorer l'état de surface.
La compensation des erreurs géométriques de la machine est également primordiale. Les techniques modernes utilisent des systèmes de mesure laser pour cartographier les erreurs de la machine et les compenser en temps réel lors de l'usinage. Cette approche permet d'atteindre des précisions submicroniques sur des pièces complexes.
Enfin, le contrôle thermique de l'environnement d'usinage joue un rôle crucial. Les variations de température peuvent entraîner des dilatations qui impactent directement la précision. Des systèmes de climatisation de haute précision et des capteurs thermiques répartis sur la machine permettent de maintenir une stabilité thermique optimale.
La précision d'usinage est le résultat d'une chaîne complexe où chaque maillon doit être optimisé, de la conception de la machine à la stratégie d'usinage.
Sélection et optimisation des outils de coupe pour pièces complexes
Le choix des outils de coupe est déterminant pour atteindre une haute précision sur des pièces complexes. Les progrès dans les matériaux et les géométries des outils ont permis des avancées significatives ces dernières années. La sélection doit prendre en compte non seulement le matériau à usiner, mais aussi la géométrie spécifique de la pièce et les exigences de précision.
Fraises en carbure monobloc pour l'usinage haute vitesse
Les fraises en carbure monobloc sont devenues incontournables pour l'usinage haute vitesse de pièces complexes. Leur rigidité exceptionnelle permet de maintenir une précision élevée même à des vitesses de rotation très importantes. Les revêtements multicouches en TiAlN ou AlCrN améliorent la résistance à l'usure et permettent d'augmenter les vitesses de coupe.
L'optimisation de la géométrie des arêtes de coupe, avec des profils variables et des brise-copeaux intégrés, contribue à réduire les efforts de coupe et à améliorer l'évacuation des copeaux. Certaines fraises intègrent désormais des canaux de lubrification interne pour un refroidissement plus efficace au niveau de l'arête de coupe.
Plaquettes PCD pour les alliages d'aluminium aéronautiques
Pour l'usinage des alliages d'aluminium utilisés dans l'aéronautique, les plaquettes en diamant polycristallin (PCD) offrent des performances inégalées. Leur dureté extrême permet d'obtenir des états de surface exceptionnels et une durée de vie d'outil considérablement accrue. Les géométries de plaquettes spécialement conçues pour l'aluminium, avec des angles de coupe positifs et des arêtes très affûtées, permettent de réduire les efforts de coupe et d'améliorer la précision.
L'utilisation de plaquettes PCD brasées sur un corps d'outil en carbure offre un excellent compromis entre performance et coût. Les techniques modernes de fabrication permettent de réaliser des géométries complexes sur ces plaquettes, comme des brise-copeaux ou des préparations d'arête spécifiques.
Outils de coupe céramiques pour les superalliages réfractaires
L'usinage des superalliages à base de nickel ou de cobalt, utilisés dans les turbines aéronautiques, pose des défis particuliers en termes de précision. Les outils de coupe en céramique, notamment les nuances à base de nitrure de silicium (Si3N4) ou de whiskers, offrent une résistance exceptionnelle aux hautes températures générées lors de l'usinage de ces matériaux.
Ces outils permettent d'augmenter considérablement les vitesses de coupe par rapport aux carbures, tout en maintenant une excellente tenue d'arête. L'utilisation d'arrosage haute pression est souvent nécessaire pour optimiser l'évacuation des copeaux et le refroidissement de la zone de coupe.
Micro-outils pour l'usinage de précision submillimétrique
L'usinage de composants miniaturisés pour l'électronique ou le médical nécessite des micro-outils de haute précision. Des fraises en carbure d'un diamètre inférieur à 0,1 mm sont désormais disponibles, permettant de réaliser des détails microscopiques avec une précision extrême.
Ces micro-outils bénéficient de géométries optimisées par simulation numérique pour réduire les efforts de coupe et améliorer l'évacuation des micro-copeaux. L'utilisation de revêtements nanostructurés permet d'augmenter la durée de vie de ces outils fragiles et d'améliorer la qualité de surface obtenue.
Le choix judicieux des outils de coupe et leur optimisation sont essentiels pour repousser les limites de la précision dans l'usinage de pièces complexes.
Stratégies de programmation CAO/FAO avancées
La programmation des trajectoires d'outil joue un rôle crucial dans l'obtention d'une haute précision sur des pièces complexes. Les logiciels de CAO/FAO modernes offrent des fonctionnalités avancées pour optimiser ces trajectoires et simuler le processus d'usinage avec une grande fidélité.
Optimisation des trajectoires d'outil avec le logiciel Hypermill
Le logiciel Hypermill est réputé pour ses capacités d'optimisation des trajectoires d'outil en usinage 5 axes. Il intègre des algorithmes avancés qui permettent de générer des parcours d'outil fluides et continus, réduisant ainsi les marques de reprise et améliorant l'état de surface.
Une fonctionnalité particulièrement intéressante est l'usinage en spirale adaptative. Cette stratégie permet d'éviter les entrées et sorties matière brutales, sources d'imprécisions et d'usure prématurée des outils. Le logiciel adapte automatiquement la trajectoire en fonction de la géométrie de la pièce pour maintenir un engagement outil constant.
L'optimisation des mouvements hors matière est également cruciale pour réduire les temps d'usinage tout en préservant la précision. Hypermill propose des algorithmes de calcul de trajectoires sûres qui évitent les collisions tout en minimisant les déplacements inutiles.
Simulation et vérification virtuelle avec VERICUT
La simulation du processus d'usinage est devenue incontournable pour garantir la précision et éviter les collisions coûteuses. Le logiciel VERICUT permet une simulation complète de l'usinage, prenant en compte non seulement la géométrie de la pièce, mais aussi la cinématique exacte de la machine-outil.
VERICUT intègre des fonctionnalités avancées comme la détection des sous-coupes ou des surépaisseurs, permettant d'identifier les zones où la précision pourrait être compromise. Il permet également de vérifier les limites de course de la machine et d'optimiser les changements d'outils.
Un aspect particulièrement intéressant est la possibilité de simuler les déformations de l'outil sous l'effet des efforts de coupe. Cette fonctionnalité permet d'anticiper les écarts de forme potentiels et d'ajuster les paramètres d'usinage en conséquence.
Compensation dynamique des déformations avec Siemens NX
Le logiciel Siemens NX intègre des fonctionnalités avancées de compensation des déformations en temps réel. Cette approche prend en compte les déformations de la pièce et de l'outil pendant l'usinage pour ajuster dynamiquement les trajectoires.
Le système utilise des modèles de simulation par éléments finis (FEM) pour prédire les déformations en fonction des efforts de coupe. Ces informations sont ensuite utilisées pour modifier en temps réel les commandes envoyées à la machine CNC, compensant ainsi les écarts de forme induits par les déformations.
Cette technologie est particulièrement précieuse pour l'usinage de pièces à parois minces ou de grandes dimensions, où les déformations peuvent avoir un impact significatif sur la précision finale.
Techniques de fixation et de bridage pour stabilité maximale
La stabilité du montage de la pièce est un facteur déterminant pour atteindre une haute précision d'usinage. Les techniques de fixation et de bridage ont considérablement évolué pour répondre aux exigences croissantes de l'industrie.
Les systèmes de bridage modulaires offrent une grande flexibilité pour s'adapter à des géométries complexes. Ils permettent de créer des montages sur mesure avec un minimum de temps de préparation. L'utilisation de matériaux composites à haute rigidité pour les éléments de bridage contribue à réduire les vibrations et à améliorer la stabilité.
Les techniques de bridage par le vide ont gagné en popularité, notamment pour les pièces de grande taille ou à parois minces. Ces systèmes permettent une répartition uniforme des efforts de maintien, réduisant ainsi les risques de déformation de la pièce. Des pompes à vide de nouvelle génération, plus silencieuses et économes en énergie, ont facilité l'adoption de cette technologie.
Pour les pièces particulièrement complexes, les techniques de bridage magnétique offrent une solution intéressante. Elles permettent un maintien puissant sans déformation de la pièce et facilitent l'accès aux surfaces à usiner. Les systèmes les plus avancés intègrent des électro-aimants commandés numériquement, permettant un contrôle précis de la force de maintien en fonction de la zone usinée.
L'utilisation de systèmes de palettisation de haute précision permet d'optimiser les temps de changement de série tout en garantissant un positionnement répétable à quelques microns près. Ces systèmes intègrent souvent des interfaces standardisées qui facilitent l'automatisation des processus d'usinage.
Contrôle thermique et compensation des dilatations
La maîtrise des effets thermiques est cruciale pour atteindre et maintenir une haute précision d'usinage. Les variations de température peuvent entraîner des dilatations qui impactent directement les dimensions finales des pièces. Plusieurs approches complémentaires sont mises en œuvre pour contrôler ces effets.
Systèmes de refroidissement cryogénique pour l'usinage du titane
L'usinage des alliages de titane génère des températures extrêmement élevées qui peuvent compromettre la précision et accélérer l'usure des outils. Les systèmes de refroidissement cryogénique utilisent de l'azote liquide pour abaisser drastiquement la température dans la zone de coupe.
Cette technique permet non seulement d'améliorer la durée de vie des outils, mais aussi de maintenir une meilleure stabilité dimensionnelle de la pièce pendant l'usinage. Les buses de projection d'azote liquide sont intégrées directement dans le porte-outil, assurant un refroidissement ciblé et efficace.
L'utilisation du refroidissement cryogénique permet également d'augmenter les vitesses de coupe, réduisant ainsi les temps d'usinage tout en améliorant la précision finale.
Mesure laser in-process avec le système Renishaw TRS2
Le système Renishaw TRS2 permet une mesure sans contact de la température de l'outil et de la pièce pendant l'usinage. Cette technologie utilise un faisceau laser pour mesurer avec précision les variations de température en temps réel.
Les données collectées sont utilisées pour ajuster dynamiquement les paramètres d'usinage et compenser les dilatations thermiques. Le système peut également détecter les bris d'outil ou l'usure excessive, évitant ainsi les rebuts coûteux.
L'intégration de cette technologie dans le processus d'usinage permet d'atteindre une précision submicronique même sur des pièces de grande taille ou des usinages de longue durée.
Compensation thermique par modélisation FEM
La modélisation par éléments finis (FEM) des effets thermiques permet une approche prédictive de la compensation des dilatations. Des capteurs thermiques répartis sur la machine et la pièce alimentent un modèle numérique qui simule en temps réel les déformations induites par les variations de température.
Ces informations sont utilisées pour ajuster les trajectoires d'outil et les paramètres d'usinage, compensant ainsi les effets thermiques avant même qu'ils se produisent. Cette approche proactive permet d'anticiper les déformations et d'assurer une précision constante tout au long de l'usinage.
Méthodes de contrôle qualité et métrologie avancée
Pour garantir la précision des pièces usinées complexes, des méthodes de contrôle qualité et de métrologie de pointe sont indispensables. Ces techniques permettent non seulement de vérifier la conformité des pièces, mais aussi d'alimenter une boucle de rétroaction pour améliorer continuellement le processus d'usinage.
Inspection 3D par tomographie computerisée
La tomographie computerisée (CT) offre une solution non destructive pour inspecter l'intérieur des pièces usinées complexes. Cette technologie utilise des rayons X pour créer une image 3D précise de la pièce, permettant de détecter des défauts internes invisibles par d'autres méthodes.
Les systèmes CT modernes atteignent des résolutions submicroniques, permettant de mesurer avec précision les dimensions internes, les épaisseurs de paroi et même la porosité des matériaux. Cette technique est particulièrement précieuse pour les pièces aérospatiales ou médicales où l'intégrité structurelle est critique.
L'analyse des données CT peut être automatisée grâce à des algorithmes d'intelligence artificielle, accélérant le processus d'inspection et améliorant la détection des anomalies subtiles.
Mesure optique sans contact avec ATOS ScanBox
Le système ATOS ScanBox de GOM représente une avancée majeure dans la métrologie optique 3D. Cette cellule de mesure automatisée utilise la projection de franges et la stéréo-photogrammétrie pour capturer rapidement la géométrie complète des pièces usinées.
Avec une précision pouvant atteindre quelques microns, l'ATOS ScanBox permet de comparer directement les pièces usinées à leur modèle CAO, générant des cartes de déviation en couleur pour une interprétation rapide des résultats. La possibilité de programmer des séquences de mesure automatisées facilite le contrôle en série de pièces complexes.
Cette technologie est particulièrement adaptée aux pièces de forme libre ou aux composants flexibles difficiles à mesurer avec des méthodes de contact traditionnelles. Elle permet également d'optimiser les processus d'usinage en fournissant des données précises sur les déformations et les tolérances.
Analyse des contraintes résiduelles par diffraction de rayons X
L'usinage de pièces complexes peut induire des contraintes résiduelles qui affectent la stabilité dimensionnelle et les performances mécaniques. La diffraction de rayons X (DRX) offre une méthode non destructive pour mesurer ces contraintes avec une grande précision.
Cette technique analyse les déformations du réseau cristallin du matériau pour quantifier les contraintes internes. Les systèmes DRX portables permettent désormais d'effectuer ces mesures directement sur les pièces usinées, sans nécessiter de prélèvement d'échantillons.
L'analyse des contraintes résiduelles par DRX est particulièrement importante pour les composants aéronautiques ou les implants médicaux, où la fatigue et la corrosion sous contrainte peuvent avoir des conséquences critiques. Elle permet d'optimiser les paramètres d'usinage pour minimiser ces contraintes et améliorer la durabilité des pièces.